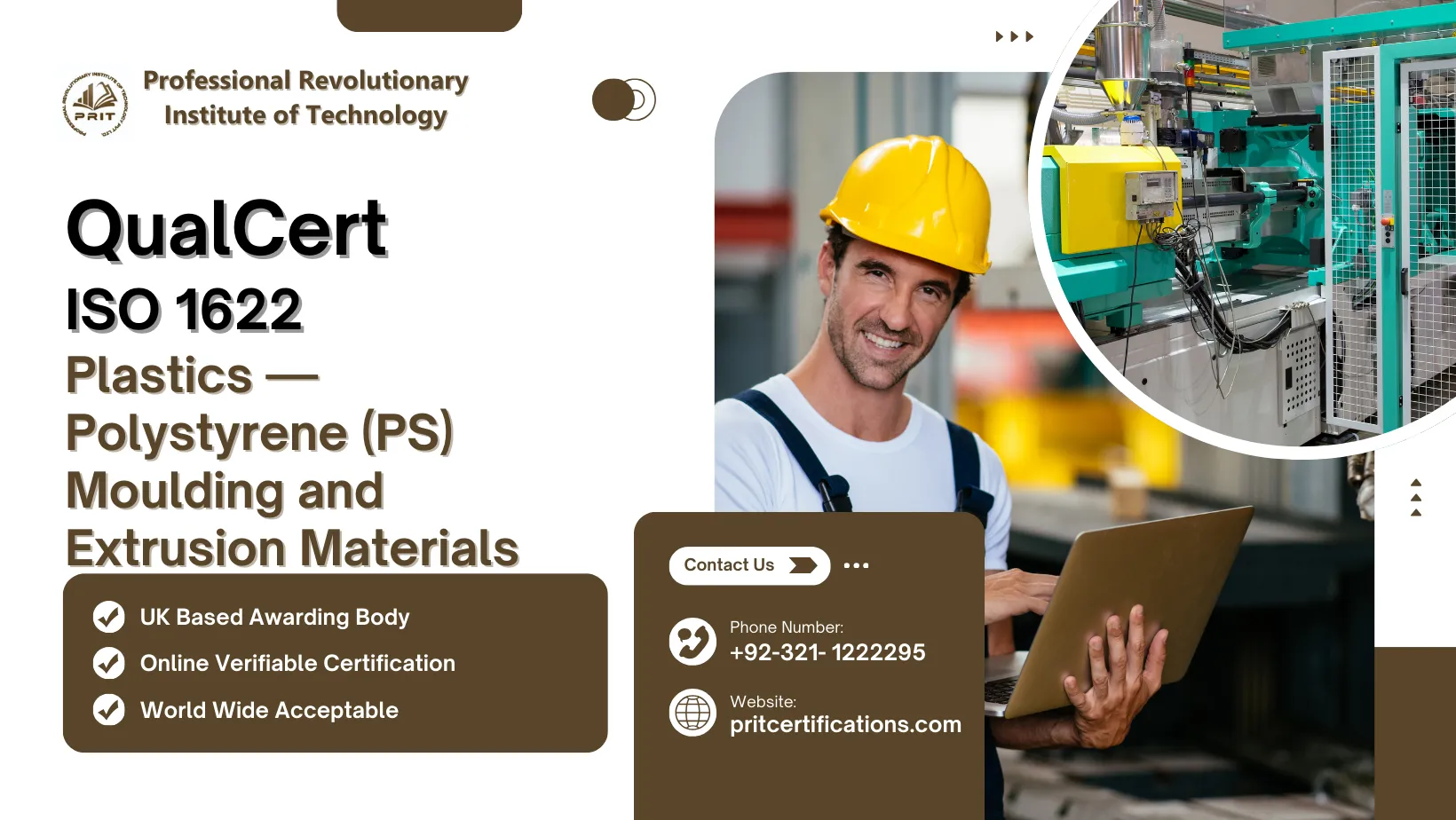
ISO 1622 is an international standard that specifically addresses the moulding and extrusion materials of Polystyrene (PS), a widely used plastic material in various industries. This standard sets out the specific requirements for polystyrene (PS), which is known for its excellent clarity, ease of processing, and versatility in both injection moulding and extrusion applications.
Polystyrene is a synthetic aromatic polymer made from the monomer styrene. It is one of the most widely used plastics in the world, found in a variety of applications ranging from packaging, food containers, and consumer products to insulation materials, and more. Polystyrene can be produced in various forms:
- General Purpose Polystyrene (GPPS): Transparent and rigid, commonly used for packaging and consumer products.
- High Impact Polystyrene (HIPS): Modified with rubber to improve impact resistance, commonly used in appliances, toys, and medical devices.
- Expandable Polystyrene (EPS): Often used in foam products like packaging, insulation, and disposable cups.
ISO 1622 defines the requirements for polystyrene (PS) moulding and extrusion materials, ensuring consistency, quality, and suitability for the intended manufacturing processes. This standard specifies the physical properties, testing methods, and characteristics necessary for producing reliable PS products.
ISO 1622 is essential for manufacturers and businesses working with polystyrene materials, as it ensures that the materials conform to specific standards of quality and performance. It enables consistent production quality and reduces the risks of material defects during the manufacturing process.
Key Requirements of ISO 1622
Some of the key requirements outlined in the ISO 1622 standard for polystyrene moulding and extrusion materials include:
- Material Properties:
- Density: Specific density values for PS materials are outlined to ensure uniformity and suitability for molding and extrusion.
- Melt Flow Index (MFI): This measures the flow characteristics of PS when molten. MFI is important for determining the material’s processability during injection molding or extrusion.
- Mechanical Properties: The standard defines essential mechanical characteristics like tensile strength, flexural modulus, and impact resistance, ensuring PS products meet the strength and durability requirements of various applications.
- Appearance and Surface Quality:
- Clarity: For general-purpose polystyrene, clarity is an important characteristic, especially for transparent applications such as packaging.
- Surface Finish: The surface of the final product must meet specific criteria for smoothness, which is essential for both aesthetic purposes and functional uses.
- Additives:
- Stabilizers, Fillers, and Coloring Agents: The standard specifies acceptable additives that can be incorporated into polystyrene to improve processing characteristics or to achieve specific properties, like UV resistance or color.
- Thermal and Electrical Properties:
- Thermal Resistance: The material must retain its mechanical properties under varying temperature conditions.
- Electrical Insulation: Polystyrene is often used in applications where electrical insulation is needed, and its performance in electrical applications is governed by the standards outlined in ISO 1622.
- Testing and Compliance:
- Testing Procedures: The standard specifies standardized testing methods for assessing the performance of PS materials in terms of mechanical strength, impact resistance, and flow properties.
- Sample Testing: Manufacturers are required to conduct regular testing of their PS materials to ensure they comply with the specifications detailed in ISO 1622.
- Packaging and Labeling: Proper identification and handling procedures, including labeling of polystyrene materials, are critical for ensuring traceability and quality control during manufacturing and transportation.
Study Units
- Introduction to Polystyrene (PS) Moulding and Extrusion
- Material Properties and Quality Control Standards
- Extrusion and Moulding Process Techniques
- Defects, Testing, and Troubleshooting in PS Processing
- Regulatory Compliance and Environmental Considerations
Applications of ISO 1622-Compliant Polystyrene Materials
Polystyrene materials that comply with ISO 1622 are used in a variety of applications across different industries. Some common uses include:
- Packaging:
- Containers: PS is used to make clear plastic food containers, such as yogurt cups, take-out containers, and other packaging for consumables.
- Blister Packs: Commonly used for packaging electronics, pharmaceuticals, and small consumer goods.
- Consumer Products:
- Toys and Household Items: Polystyrene is used in the production of plastic toys, kitchenware, and office supplies due to its versatility and ease of processing.
- Cosmetic Packaging: Polystyrene is used in the packaging of beauty and personal care products due to its transparency and rigidity.
- Electronics:
- Electrical Insulation: Polystyrene is used as an insulating material in electronic devices, providing both electrical and thermal protection.
- Automotive Parts:
- Interior Components: PS materials are used in car interiors for dashboard components, trim, and other aesthetic features that require rigidity and dimensional stability.
- Building and Construction:
- Insulation: Expandable Polystyrene (EPS) is commonly used in insulation materials in the construction industry, providing thermal resistance and reducing energy costs.
Benefits of Complying with ISO 1622
- Quality Assurance: ISO 1622 ensures that the polystyrene materials used in manufacturing processes meet globally recognized quality standards, leading to more reliable end products.
- Consistency: By adhering to the standards set by ISO 1622, manufacturers ensure that the physical properties, mechanical strength, and appearance of the material are consistent across batches, reducing the potential for defects and ensuring customer satisfaction.
- International Trade and Acceptance: Compliance with ISO standards, including ISO 1622, ensures that polystyrene materials are acceptable in international markets. Manufacturers can confidently export products worldwide, knowing that they meet the necessary requirements.
- Cost Efficiency: Standardized materials allow manufacturers to streamline production processes, reduce waste, and improve cost efficiency. This is particularly important in industries where material performance and quality are directly tied to overall production costs.
- Environmental Considerations: With growing environmental concerns, the ISO standard ensures that manufacturers take steps to minimize the environmental impact of polystyrene materials through the responsible use of additives and efficient production processes.
ISO 1622 is a vital standard for manufacturers, suppliers, and end-users of polystyrene (PS) materials. It ensures that PS materials used for moulding and extrusion meet the required mechanical, thermal, and aesthetic properties while adhering to global quality standards. By following ISO 1622, manufacturers can ensure the reliability, safety, and performance of their products, enhance the efficiency of production, and maintain consistency in their product offerings across international markets.